Leak on the back of the tank
My GIV-B5 powered Jungmann vibrates more than I’d like, and this may have caused cracks in the nose bowl, some side panels and a few cracks in the fuel tank.
Latest crack (at 470 hours) on tank bottom.
I welded one crack on the tank bottom before I assembled the plane; had another show up on the bottom at about 200 hours that was repaired with PRC sealant on the inside and a composite patch on the outside.; the third occurred half way up the back of the tank at 320 hours and was also fixed with an exterior carbon-fibre patch; and the latest showed up on the bottom just aft of the fuel pick-up boss. I took the tank out and had the two most recent cracks welded, then pressure testing revealed more cracks in the same area so my welder re-enforced the entire area around the boss.
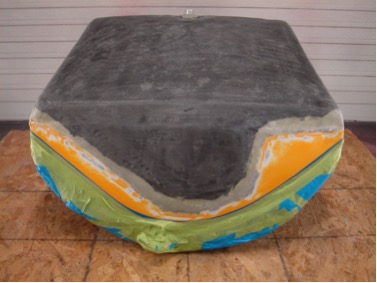
Carbon fibre “sandwich”.
With no more leaks we then covered the bottom with a carbon-fibre sandwich (one layer of fiberglass against the aluminum bottom and lower sides, 3 layers of CF and another layer of fiberglass). This should improve rigidity and hopefully reduce cracking. It was then painted and actually looked pretty good!
Time to re-install the tank: It wouldn’t fit! The bottom of the tank had ballooned outwards so much that it rested on fuselage cross-member tubes instead of the 4 corner supports. The top of the tank was one centimeter higher than the adjoining cowls and could not be made to fit with the existing cowlings. It seems a faulty pressure gage may have allowed about 5 PSI into the tank instead of the planned 2 PSI which forced out the bottom. This was not discovered prior to applying the composite sandwich or painting.
Several options were considered but the quickest was thought to be a new tank.
So began another adventure in Bücker maintenance. I found 2 tanks - close to where I live - in order to see which one would fit the best and discovered that quality control was again lacking in the physical size and shape of Spanish fuel tanks. One wouldn’t fit into the 4 support pads because it’s lateral width was one centimeter wider than the pads could restrain. The other tank appeared to have been media blasted on the inside with a fine sand, however it fit in the pads but was about one inch shallower (total height) than the other tanks, and the four corners were all different heights from the actual bottom.
Tank needs a new flop tube boss.
I chose the second one and in so doing had to make and weld in place a new boss for the flop tube (the original had been scavenged to make another tank); and shorten the fuel tank sight gage by one inch as it hit the higher bottom and could not be fully screwed into its mounting thread.
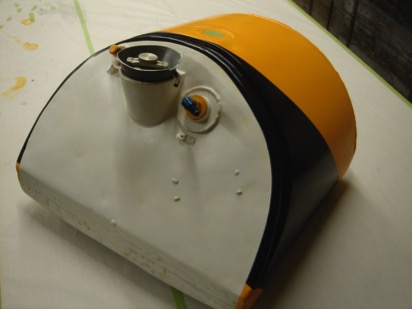
Tank ready to install.
Pressure testing this tank (with a new, very accurate gage) revealed no leaks so after it was cleaned I added a carbon-fibre sandwich to the bottom and painted it. It proved to be quite problematic to make it fit with the existing cowls but we did manage to get it all back together and have put 30 hours on it so far.
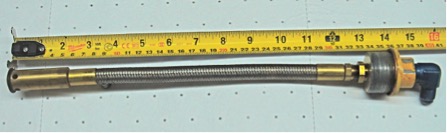
Flop Tube – too long.
The story is not finished!
I started hearing a strange, rattling noise at about 1000 RPM – as if a panel was flapping in the prop-wash - and investigation revealed the fuel tank flop tube was resting on the bottom of the tank and wearing both the brass weight on the flop tube and the aluminum tank bottom. This 13 inch flop tube is from Aircraft Spruce and has a brass weight that is long enough to enable shortening.
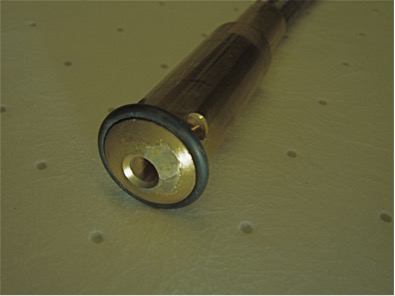
Fortunately not much damage had been done, and I have shortened the flop tube brass end by one inch. It now weighs 45 grams less and does not touch the bottom! Aerobatic flight testing has confirmed minimum fuel quantity for unusual attitude engine operation is the same as before the surgery.
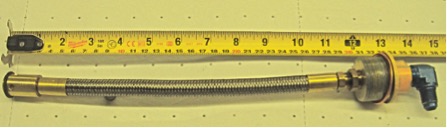
Brass end weight (at left) shortened by one inch
Several operators have reported fuel tank cracks, but the worst incident that we are aware of happened in England where the bottom of a Jungmann tank let go during flight and soaked the front seat passenger with avgas. Fortunately there was no fire and they were able to land without damage to the crew or plane. I’m not aware whether the engine was shut down or continued to run – I hope I never have to make that decision….
(Woody Menear had an engine stoppage that was caused by metal flakes from the fuel tank. His flop-tube weight had been banging on the inside of the tank and chipping off pieces of the metal - SB)