Just a quick heads up on progress with production of new 150 hp Tigre piston sets. I have the first production set but have not had the time to fit them yet with work and all the other rectification work. Photos attached of the complete set.
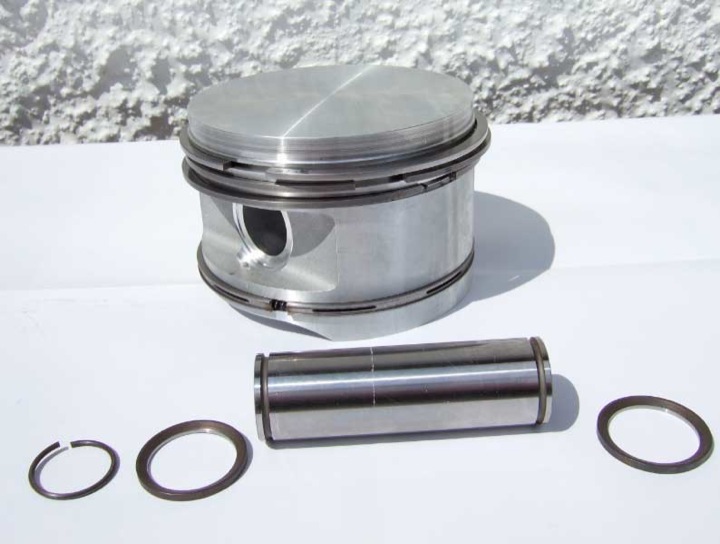
They are machined from solid RR2618 (Rolls Royce aircraft spec alloy) bar which is used in almost all aircraft piston manufacture here now from Merlin to Genet. Machining from solid is far safer than casting or forging, its never going to break up in flight. They are as close a copy of the pistons made for the Spanish in 1971 by Borgo pistons which were forged as opposed to the earlier pistons made in late 40s/early 50s also by Borgo which were cast.
By 1971 they had deleted the undercut under the gudgeon pin bosses which is dissapproved of in modern thinking as there is prevalence to cracks here with undercuts. The interior pocket design is as close as possible to the original as maching from solid will allow. They weigh the same as the originals.The gudgeon pins, washers, circlips and compression rings are exact copies of the original Spanish, Joe Rosenberg lent some unused examples for copying.
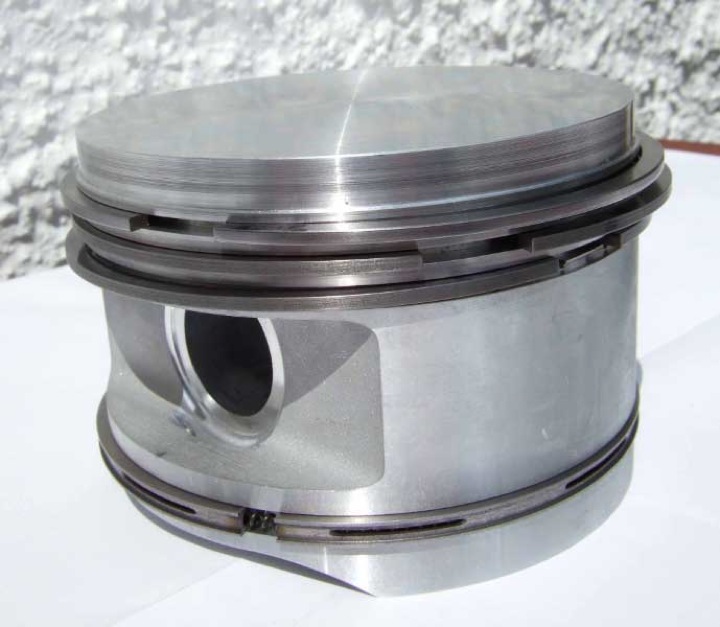
The oil control ring is modified though the groove in the piston is the same size as the original. It is a conformal sprung ring ie without its spring it would hide in the groove and have no effect, this means the effect is variable by simply modifying the length of the spring. There is alot of experience with using sprung oil control rings in Gipsy Major engines and experience has shown that too harsh a spring can cause excessive bore wear.
The prototypes have been set by the manufacturers FJ Engineering to give what they think will be optimum oil control with minimal wear but this can be adjusted depending on experience. A conformal sprung ring will apparently accommodate uneven variations in the bore most effectively which should be useful in older engines.
Experience with Gipsy Majors has shown that when modern oil control rings are fitted to standard pistons, due to the reduced oil quantity reaching the compression rings there is less impact absorption by the oil film of the ring movement against the ring groove wall and therefore the grooves get worn oversize very quickly. The pistons were made originally with very wide ring grooves even for an air cooled engine so that the rings would remain highly mobile to break out the carbon formation caused by the excessive amounts of oil reaching the compression rings (and your combustion chamber). For this reason the compression ring grooves have been very slightly reduced in width in the new pistons by betweem 0.10 to 0.07 of a mm to compensate. A standard original oil ring could be fitted but the compression ring grooves would need to be opened out again.
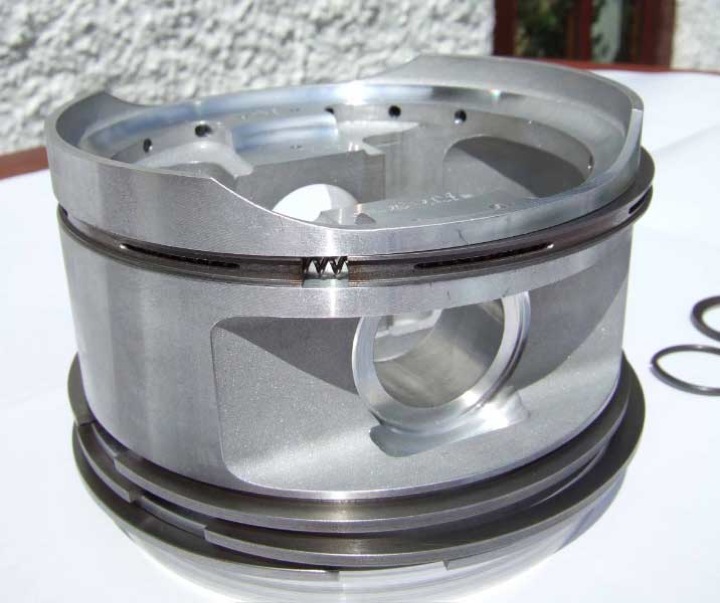
The other mod is a small waist around the piston land which is a way to try and avoid damage to the land due to lead build up in the combustion chamber. This should cause the lead deposits to be less compacted by the piston action and more able to break off. The loss of material is compensated for by a 1mm increase in the height of the crown. It would be easy to delete this from the CNC program if it does not work but its worth a try on the prototype.
The whole set has been made by FJ Engineering (http://www.fj-engineering.co.uk ) who have alot of experience with all sorts of piston manufacture and the company has its origins with Wellworthy Engineering who were the manufacturers for numerous aircraft pistons including the DH Gipsy Major etc. Some of the staff date from the Wellworthy days and so have first hand experience of aircraft work. They have made pistons for several aircraft over the last few years including Gipsy, Renault, Cirrus Bombardier, Genet, Merlin and are currently making ring sets for the Centaurus engines in the Royal Navy Historic Flight Sea Furies. They make pistons for many classic and vintage car clubs and also for various military engines in armoured cars etc which have worn out their entire spares stock in the dust of Iraq and Afghanistan.
Unfortunately this does mean that nothing happens quickly as they are always 'up to here' with the latest order. The Tigre pistons are machined from solid on CNC and the finished on a piston lathe to give them the beer barrel shape and round crown/oval skirt which is impossible to do any other way (piston lathes are somewhat rare in ther UK as are the lathe cams to go with it).
The plans have been approved by the UK Light Aviation Association, the airworthiness authority for UK registered Jungmanns. Once I have rebuilt my engine I wiil need to do a test flying program of about 15 hours before they are fully approved by the LAA, subject to any problems and mods/demods that become necessary.
There have been 2 Jungmann engine failures in Europe in the last few months due to a gudgeon pin circlip coming adrift complete with its washer. The new circlips are already therefore finding a home as the fit of the originals is often poor due to them having been used so many times.
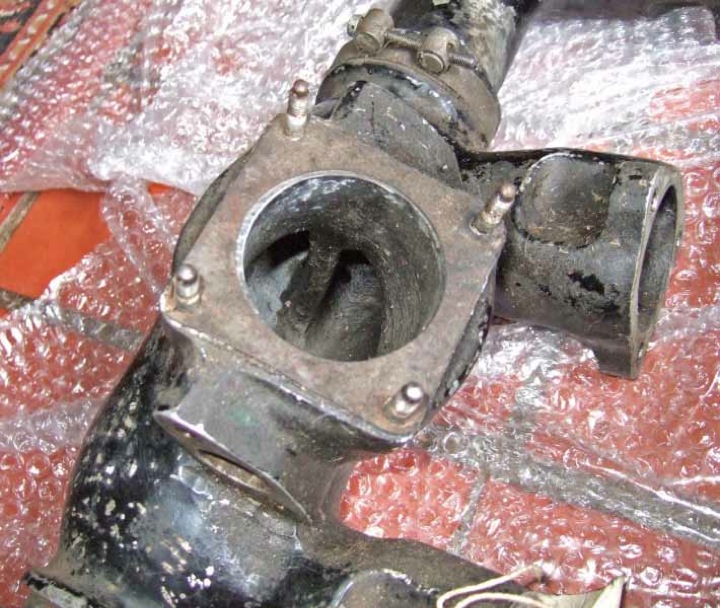
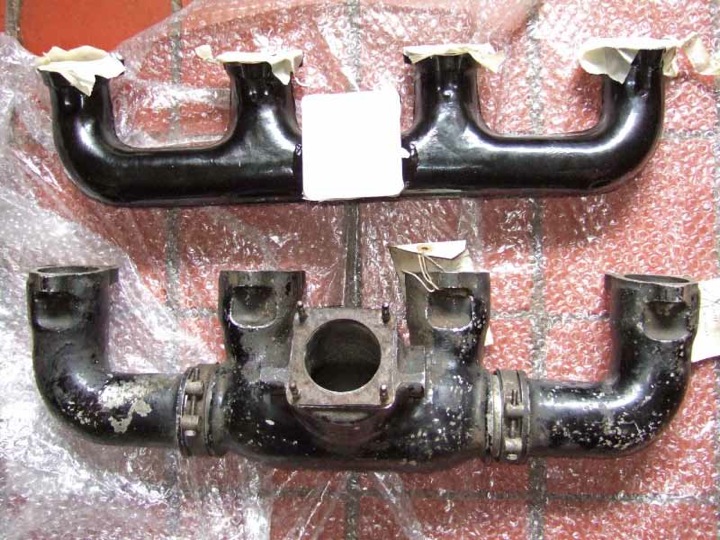
Plans are also in hand to make a modern copy of the original split duct Tigre induction manifold which we think will benefit Ellison TBI fitted aircraft alongside the existing plenum chamber mod (photo of orginal attached)
Regards
John Hopkins G-BWHP (S4-A-07)
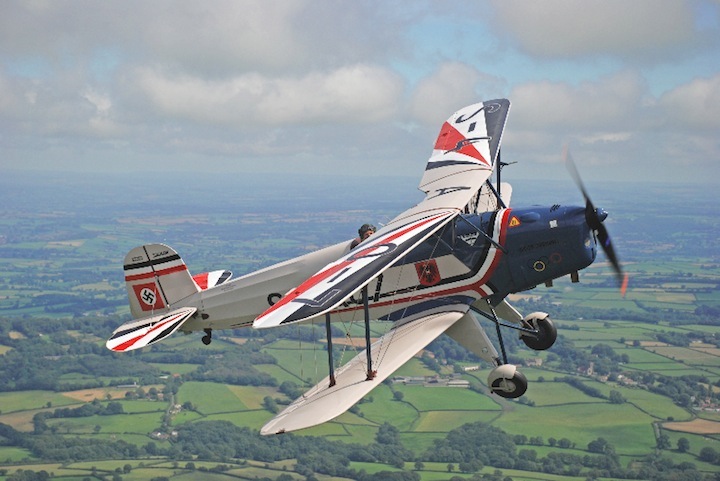